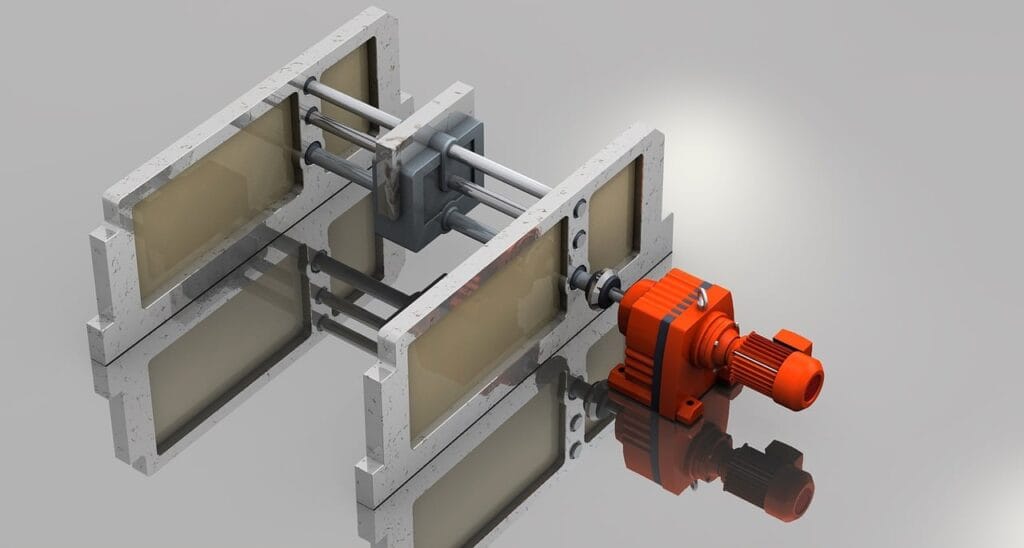
En el competitivo mundo industrial actual, la optimización de procesos se ha convertido en una necesidad imperiosa para las empresas que buscan mantenerse a la vanguardia. Ya no basta con simplemente producir; hay que hacerlo de manera inteligente, eficiente y sostenible. La optimización de procesos industriales es el camino hacia ese futuro prometedor.
Pero, ¿qué implica realmente esta optimización y cómo puede beneficiar a tu empresa? En este artículo, vamos a revisar el mundo de la mejora continua y descubrir cómo implementar estrategias que pueden transformar radicalmente tu negocio.
Optimización de procesos industriales: Fundamentos y beneficios
La optimización de procesos industriales es mucho más que una simple moda pasajera. Se trata de un enfoque sistemático para mejorar la eficiencia, reducir costos y aumentar la calidad en todos los aspectos de la producción industrial. Pero, ¿cuáles son los beneficios concretos que puede aportar a tu empresa?
- Reducción de costos: Al eliminar ineficiencias y desperdicios, puedes ver una disminución significativa en tus gastos operativos.
- Aumento de la productividad: Procesos más eficientes significan más unidades producidas en menos tiempo.
- Mejora de la calidad: La optimización no solo se trata de velocidad, sino también de precisión y excelencia en el producto final.
- Mayor satisfacción del cliente: Productos de mejor calidad y entregas más rápidas se traducen en clientes más felices.
- Ventaja competitiva: Empresas optimizadas están mejor posicionadas para enfrentar los desafíos del mercado.
Pero la pregunta del millón es: ¿cómo empezar con la optimización? El primer paso es el análisis de flujo de valor.
Análisis de flujo de valor: Identificando oportunidades de mejora
El análisis de flujo de valor (VSM, por sus siglas en inglés) es una herramienta poderosa que permite visualizar todo el proceso productivo, desde la recepción de materias primas hasta la entrega del producto final al cliente. Es como tener un mapa detallado de tu fábrica, donde cada paso está bajo la lupa.
Para implementar un VSM efectivo:
- Forma un equipo multidisciplinario.
- Mapea el estado actual del proceso.
- Identifica actividades que agregan valor y las que no.
- Diseña un estado futuro ideal.
- Desarrolla un plan de acción para alcanzar ese estado.
¿Sabías que las empresas que implementan VSM regularmente reportan mejoras de eficiencia de hasta un 30%? Es como encontrar un tesoro oculto en tu propia planta de producción.
Automatización inteligente: El futuro de la producción industrial
La automatización ya no es ciencia ficción; es una realidad que está transformando fábricas en todo el mundo. Pero no se trata solo de reemplazar trabajadores por máquinas. La automatización inteligente implica integrar sistemas que piensan, aprenden y se adaptan.
Beneficios de la automatización inteligente:
- Reducción de errores humanos
- Aumento de la velocidad de producción
- Mejora en la consistencia de la calidad
- Capacidad para operar 24/7
Sin embargo, la implementación de la automatización debe ser estratégica. No todo proceso debe ser automatizado. La clave está en identificar dónde la automatización puede aportar el mayor valor.
¿Te preocupa el costo inicial? Piensa en esto: aunque la inversión inicial puede ser significativa, el retorno de inversión (ROI) suele ser rápido. Muchas empresas reportan un ROI completo en menos de 18 meses.
Lean Manufacturing: Eliminando desperdicios y maximizando recursos
El Lean Manufacturing, o producción ajustada, es una filosofía que busca minimizar el desperdicio sin sacrificar la productividad. Se origina en el sistema de producción de Toyota y ha revolucionado la industria desde entonces.
Los principios clave del Lean Manufacturing incluyen:
- Identificar valor: ¿Qué valora realmente el cliente?
- Mapear el flujo de valor: Similar al VSM, pero con un enfoque en eliminar desperdicios.
- Crear flujo: Asegurar que los procesos fluyan sin interrupciones.
- Establecer pull: Producir solo lo que se necesita, cuando se necesita.
- Buscar la perfección: Mejora continua en todos los aspectos.
Un dato interesante: las empresas que implementan Lean Manufacturing reportan reducciones de hasta un 50% en el tiempo de ciclo de producción. ¿Te imaginas lo que eso podría significar para tu empresa?
10 Tipos de Software Administrativo Esenciales para Tu Negocio
Gestión de la calidad total: Excelencia en cada etapa del proceso
La Gestión de la Calidad Total (TQM, por sus siglas en inglés) no es solo un departamento o una fase del proceso; es una filosofía que impregna toda la organización. Se trata de crear una cultura donde la calidad es responsabilidad de todos.
Elementos clave de la TQM:
- Enfoque en el cliente
- Liderazgo comprometido
- Participación de todos los empleados
- Enfoque basado en procesos
- Mejora continua
- Toma de decisiones basada en hechos
¿Por qué es tan importante? Porque la calidad no es negociable en el mercado actual. Los clientes esperan excelencia, y las empresas que no pueden proporcionarla simplemente quedan fuera del juego.
Mantenimiento predictivo: Anticiparse a los problemas para evitar paradas
Imagina que pudieras predecir cuándo una máquina va a fallar antes de que ocurra. Eso es exactamente lo que ofrece el mantenimiento predictivo. Utilizando sensores, análisis de datos y aprendizaje automático, podemos anticiparnos a los problemas y abordarlos antes de que causen interrupciones costosas.
Beneficios del mantenimiento predictivo:
- Reducción de tiempos de inactividad no planificados
- Aumento de la vida útil de los equipos
- Optimización de los costos de mantenimiento
- Mejora de la seguridad en el lugar de trabajo
¿Sabías que el mantenimiento predictivo puede reducir los costos de mantenimiento hasta en un 30% y eliminar las averías casi por completo? Es como tener una bola de cristal para tu maquinaria.
Integración de tecnologías 4.0: IoT, IA y big data en la industria
La Industria 4.0 no es el futuro; es el presente. La integración de Internet de las Cosas (IoT), Inteligencia Artificial (IA) y análisis de big data está creando fábricas inteligentes capaces de adaptarse en tiempo real a las cambiantes condiciones de producción.
¿Cómo puede beneficiarte la Industria 4.0?
- Monitoreo en tiempo real de la producción
- Optimización automática de procesos
- Mantenimiento predictivo más preciso
- Personalización masiva de productos
- Mejor trazabilidad y control de calidad
Un dato impactante: según un estudio de McKinsey, las empresas que han adoptado tecnologías de la Industria 4.0 han visto aumentos de productividad de hasta un 30%. ¿No es hora de subirse a este tren?
Capacitación y empoderamiento del personal: El factor humano en la optimización
En medio de toda esta tecnología, es fácil olvidar el componente más importante de cualquier proceso industrial: las personas. La optimización de procesos no puede tener éxito sin un personal capacitado y empoderado.
Estrategias para el desarrollo del personal:
- Programas de formación continua
- Fomento de la cultura de mejora continua
- Sistemas de sugerencias de empleados
- Equipos de resolución de problemas multifuncionales
- Liderazgo participativo
Recuerda: la tecnología es una herramienta, pero son las personas quienes impulsan la innovación y la mejora continua.
Medición y mejora continua: KPIs para el éxito a largo plazo
«Lo que no se mide, no se puede mejorar», dijo alguna vez Peter Drucker. Y tenía razón. La optimización de procesos industriales requiere un sistema robusto de medición y seguimiento de KPIs (Indicadores Clave de Desempeño).
Algunos KPIs cruciales para la optimización de procesos:
- Eficiencia Global del Equipo (OEE)
- Tiempo de ciclo
- Tasa de defectos
- Tiempo medio entre fallos (MTBF)
- Rendimiento de entrega a tiempo
- Rotación de inventario
La clave está en no solo medir, sino actuar sobre esos datos para impulsar la mejora continua.
Casos de éxito: Empresas que han transformado sus procesos
Nada ilustra mejor el poder de la optimización de procesos industriales que los casos de éxito reales. Veamos algunos ejemplos inspiradores:
- Toyota: Pionera del Lean Manufacturing, Toyota logró reducir sus tiempos de producción en un 50% y aumentar su productividad en un 300% a lo largo de dos décadas.
- Siemens: Implementando tecnologías de la Industria 4.0, Siemens logró aumentar su productividad en un 30% en su planta de Amberg, Alemania.
- Harley-Davidson: Adoptando prácticas de Lean Manufacturing y Six Sigma, Harley-Davidson redujo su tiempo de producción de 21 días a 6 horas.
Estos casos demuestran que, con el enfoque adecuado, la optimización de procesos puede llevar a mejoras dramáticas en eficiencia y productividad.
Conclusión de optimización de procesos industriales
La optimización de procesos industriales no es un destino, sino un viaje continuo. Es un compromiso con la excelencia que requiere dedicación, inversión y una mentalidad abierta al cambio. Pero los beneficios son innegables: mayor eficiencia, mejor calidad, costos reducidos y una ventaja competitiva sostenible.
¿Estás listo para llevar tu empresa al siguiente nivel? La optimización de procesos industriales es el camino, y el momento de empezar es ahora. Recuerda, en el mundo industrial de hoy, la única constante es el cambio. Las empresas que abrazan la optimización no solo sobreviven; prosperan.
¿Te ha resultado útil este artículo acerca de optimización de procesos industriales? ¿Tienes experiencias propias con la optimización de procesos que te gustaría compartir? No dudes en dejar tus comentarios y compartir este artículo con tus colegas. Juntos, podemos impulsar una revolución de eficiencia en la industria.
Tabla de Contenidos
- Optimización de procesos industriales: Fundamentos y beneficios
- Análisis de flujo de valor: Identificando oportunidades de mejora
- Automatización inteligente: El futuro de la producción industrial
- Lean Manufacturing: Eliminando desperdicios y maximizando recursos
- Gestión de la calidad total: Excelencia en cada etapa del proceso
- Mantenimiento predictivo: Anticiparse a los problemas para evitar paradas
- Integración de tecnologías 4.0: IoT, IA y big data en la industria
- Capacitación y empoderamiento del personal: El factor humano en la optimización
- Medición y mejora continua: KPIs para el éxito a largo plazo
- Casos de éxito: Empresas que han transformado sus procesos
- Conclusión de optimización de procesos industriales